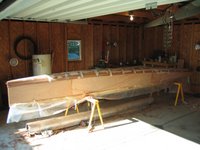
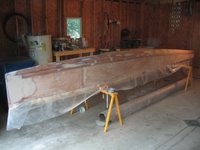
So it’s been a while since my last post. Well a lot has happened. In the last post I had started planeing and faring the hull getting it ready to fiberglass. This took a lot longer then I thought it was going to as, once again, I really didn't know if I was doing it right. Well, I did it right, at least for my first time. Fairing the hull (taking out any dips and hollows) involves a lot of sanding, spreading fairing putty (a mixture of epoxy and a special filler), sanding some more and repeating this process several times. I finally got it as good as I was going to and was ready to glass.

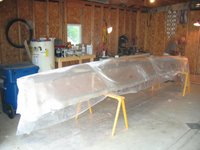

And... last Saturday was a good day. My friend John and I (mostly John) fiber glassed the first hull. It took about three hours and went really smooth. To do this we first spread a very thin coat of epoxy to seal the wood then laid the glass on the hull and cut the cloth to the size we needed. The glass cloth is a weave which we needed to lay on a 45 degree angle to the center line of the boat allowing for maximum strength. In doing this we used 3-4 pieces of cloth overlapping by about 1 inch. After the cloth was cut and positioned we rolled back the overlap and began spreading epoxy on the first section. Again this is a very thin coat of epoxy, just enough to wet the cloth and make it stick to the hull. We repeated this process for all the pieces until it was covered.
Since Saturday I have rolled one two more coats of epoxy to eliminate the texture of the cloth and I am now ready to pull the first hull off the mold. Finally! Then I get to repeat the process again for the second hull. Hopefully, since I know how to do it now, it will go a lot quicker.
So... tomorrow I am planning on pulling the hull off and placing it in the holding jig. This is a "table" of sorts with a hole cut in it in the plan view (looking down onto the top of the hull) shape of the hull. This will hold the hull as I glass the inside and lay in all of the internal structure of the hull.
I hope to have pics of the hull coming of Monday.