So, last summer I started on my first attempt of building my "A" cat (an "A" class catamaran is '18 long, 7'6 1/2" wide multihull sailboat with 150 square feet of sail. I will be adding links to "A" cat websites soon for those who want to see a complete version of what I am building). My friend, John, told me of three techniques for building the cat. The first is a "stitch and glue" process. this involves joining two flat panels (cut to specific shapes) at the keel (boat term) with plastic zip ties, gluing them together with epoxy and fiberglass tape, then folding them into shape (see photos). The second is strip build, using cedar strips that are 3/4 x 1/4, and lay them together over a form. The third is vacuum bagging. This is a light weight construction of very thin ply-wood with a honeycomb core. It’s then laid over a form and a plastic bag is slipped over it, sealed and the air sucked out of it. I chose to use the stitch and glue method for the first attempt.
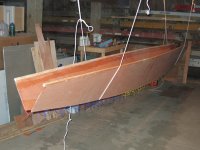
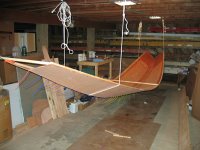
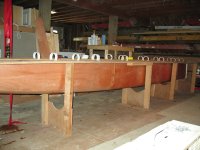
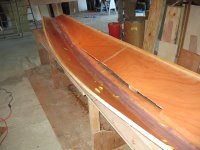
The first hull of the first attempt went ok with a minor problem after folding the hull up. I managed to crack the transom (boat term again). This was pretty easy to fix in the end using some epoxy mixed with some filler and sanded to shape. The second hull, however, did not fair so well. While folding it into shape I managed to put a 9 foot crack down the middle. That makes it kind of difficult to sail. This happened in the fall at which point I needed to clean things up as the family, who was letting me use a portion of their barn needed it to store their own boat for the winter.
It is now spring, I just bought a new house with a huge garage (yes I had the boat in mind while looking at houses) and I'm ready for the second attempt. This time I'm using a modified version of the strip build method. The hull sides will be made up of 4mm Okume ply-wood while the rounded hull bottom will be the strips. This will be a bit easier in construction and certainly less stress on the wood.
1 comment:
Post a Comment